「利益が見えない」から脱却する──中堅製造業に必要な“個別原価管理”の考え方
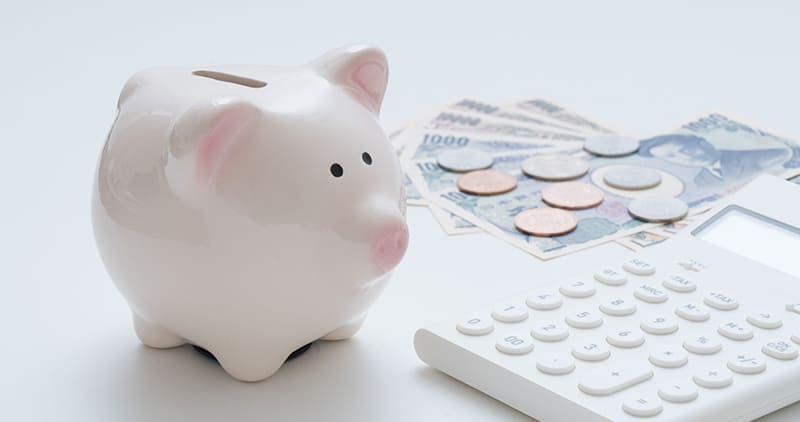
1.はじめに
中堅・中小規模の製造業を取り巻く経済環境は、今、かつてないスピードで変化しています。
ロシア・ウクライナ情勢や円安などによる原材料費やエネルギーコストの高騰、中長期的には熟練技能者の高齢化や人手不足も進行しており、これまでの業務の延長線上では収益を維持することすら難しい状況にあります。
加えて、顧客ニーズの多様化を背景に、多品種・小ロット・短納期といった要求が当たり前になりました。技術力や品質は前提とされ、競争の軸は「いかに柔軟に・効率的に・利益を確保できるか」へと移りつつあります。
こうした環境下で、製造業の経営者や管理部門が共通して抱える悩みがあります。
「この案件、本当に儲かっているのかが分からない」
「なぜ赤字になったのか説明できない」
現場では懸命にコストを抑えて生産しているにも関わらず、月次決算が出る頃にはすでに手遅れ、ということも珍しくありません。
このように、事業運営の根幹であるはずの「原価」や「利益」が“タイムリーに見えていない”という現状は、多くの中堅・中小製造業に共通する構造的な課題です。
実際、従来のように総額ベースの売上や費用を部門単位で把握しているだけでは、どの仕事が収益を生んでいるのか、逆に損失を生んでいるのかまでは見えません。特に、受注ごとに仕様や加工内容が異なる個別生産型の企業では、案件ごとの原価と利益の“見える化”=個別原価管理の仕組みが不可欠になります。
本コラムでは、こうした「利益が見えない」状況から脱却するために、中堅製造業が取り組むべき“個別原価管理”の考え方と、その実践方法について、ERPを活用した事例も交えながら詳しく解説していきます。
2.個別原価管理とは何か?─利益構造を“見える化”するための基礎知識
「原価管理はしているつもりだが、なぜか赤字が出る」「もっと正確に見積もりたいのに、原価が分からない」こうした声は、案件ごとに仕様が異なる個別受注型・多品種少量生産型の製造業において特に多く聞かれます。背景にあるのが、“原価の見えにくさ”という構造的な問題です。
中堅・中小製造業でよく見られるのが、月次の試算表レベルで売上と仕入・経費の差を見て利益を判断しているケースです。
しかしこの方法では、「どの案件で利益が出て、どの案件で赤字なのか」はわかりません。これでは経営判断に必要な“粒度”の情報にはなりません。
1)原価管理の二つの方式
原価計算には大きく分けて「総合原価計算」と「個別原価計算」の2種類があります。
区分 | 総合原価計算 | 個別原価計算 |
---|---|---|
対象 | 大量生産品(例:食品、化学品) | 受注生産品(例:機械、金型、部品) |
管理単位 | 製品や部門ごと | 案件(製番)ごと |
特徴 | 原価が平均化される | 案件ごとの収支が見える |
中堅製造業、とくに受注ごとに製品仕様が異なるような企業では、「個別原価計算」を導入することで、案件別に発生した材料費、工数、外注費、間接費などのコストを詳細に把握し、収支を精密に管理することが可能になります。
【個別原価の構成要素】
- 材料費(部品・資材の購入費)
- 労務費(作業者の工数・時間)
- 外注費(加工・組立の委託)
- 間接費(共通費の按分)など
2)“見える化”がもたらす経営的な意義
個別原価計算を導入する最大のメリットは、「どの案件が儲かっていて、どの案件が赤字なのか」が明確になることです。
これにより、以下のような重要な意思決定が可能になります。
見積精度の向上 :過去案件の実績に基づいた根拠ある積算
利益率の確保 :採算の合わない案件の受注抑制や条件交渉
原価改善の着眼点:材料ロスや外注コスト、工数超過などの要因特定
製番別の利益管理:営業・製造・経営陣が共通の原価意識を持つ基盤に
3)個別原価管理は「儲け方」を見直す起点になる
単にコストを記録するだけでなく、個別原価管理は“どこで儲け、どこで損しているか”という構造的な利益の源泉を明らかにするための仕組みでもあります。
「感覚」や「経験」に頼らない精緻な収支管理は、将来にわたって企業を支える大きな武器になります。
3.現場任せでは利益が守れない──中堅企業における原価管理の課題
「利益は出ているはずなのに、なぜか資金繰りが苦しい」「見積もりと実績が大きくズレているが、理由がわからない」こうした悩みは、多くの中堅・中小製造業が抱える共通の課題です。その根本には、属人的で断片的な原価管理の限界があります。
1)Excel管理の限界
中堅企業では、案件ごとの原価をExcelや紙の台帳で手作業集計しているケースが珍しくありません。
たとえば次のような運用がよく見られます。
- 現場担当者が材料使用量や工数を個別に記録
- 管理部門が手作業で集計し、月末に実績を確認
- 原価と売上の突合は、請求書処理ベースで実施
このような状態では、一見、管理はされているように見えても、実際には以下のようなリスクを抱えています。
リスク | 内容 |
---|---|
属人性 | 担当者の頭の中にしか原価の算出根拠がない |
遅延性 | 原価実績の把握が月末〜翌月になるため、即時対応が困難 |
精度の低下 | 工数記録が曖昧だったり、間接費の配賦が適当になりやすい |
部門間の分断 | 営業、製造、経理がそれぞれバラバラの情報を持っている |
2)情報の「つながり」がないことで判断が遅れる
特に課題なのが、原価に関する情報が生産、購買、外注、営業、経理など複数部門にまたがって存在している点です。
それぞれが独立したExcelを持ち、同じ案件に対して別の数値を扱っていれば、当然ながら精緻な原価計算は困難になります。
また、手元のExcelで管理している限り、リアルタイムでの原価の進捗確認や見積精度の検証、PDCAの高速回転は不可能です。
結果として、「気づいた時には赤字」「価格交渉の材料がなく受注せざるを得ない」という悪循環に陥ってしまいます。
3)「現場任せ」から「仕組みで守る」体制へ
原価管理を現場の経験や勘に頼る時代は、終わりを迎えつつあります。
経営層や管理部門がリアルタイムに案件ごとのコスト構造を把握し、“利益が出る仕組み”を全社で共有することが求められています。
そのためには、情報を部門横断的に一元化し、属人性を排除し、誰が見ても同じ数値で判断できる「共通の土俵」=ERPによる原価管理の仕組みが有効です。
4.ERPで変わる原価管理──業務のつながりが“利益の見える化”を実現する
個別原価管理の必要性を理解していても、実際の導入や運用となると「手間がかかるのでは?」「現場が対応できないのでは?」という不安の声が聞かれます。しかし近年では、ERP(統合基幹業務システム)を活用することで、負担を抑えながら正確な原価管理を行う環境が整いつつあります。
ここでは、ERPによる原価管理の変化を具体的に見ていきましょう。
1)業務データの「自動連携」が原価の正確性を高める
ERPの最大の特徴は、「販売」「購買」「在庫」「製造」「経理」など各業務プロセスの情報がシームレスに連携していることです。
この仕組みにより、現場で入力された情報が自動的に原価データとして集計・反映されるため、以下のような“つながった管理”が実現します。
【ERPによる原価データ連携のイメージ】
受注 → 製番発行 → 購買(部品・外注) → 作業実績(工数・仕掛品) → 出荷・売上 → 製番別損益
部門 | 入力内容 | 原価管理での活用 |
---|---|---|
営業 | 製番/受注情報 | 案件ごとの予算原価設定 |
購買 | 購買実績/仕入価格 | 材料費の実績反映 |
製造 | 作業実績(工数) | 直接作業費の集計 |
経理 | 配賦ルール | 間接費の按分と月次集計 |
このように、現場の業務の延長で入力されたデータが、原価管理に自動的につながっていくため、従来のように手作業で集計する必要がなくなります。
2)「製番管理」で案件別の損益をリアルタイムに把握
ERPでは、受注ごとに発行する「製番(製造番号)」を軸に、材料費・工数・外注費・間接費を紐づけて集計できます。これにより、案件別の損益をリアルタイムで「見える化」できます。
製番 | 顧客 | 材料費 | 外注費 | 工数費 | 間接費 | 売上 | 損益 |
---|---|---|---|---|---|---|---|
00123 | A社 | 120,000円 | 50,000円 | 80,000円 | 30,000円 | 350,000円 | +70,000円 |
00124 | B社 | 200,000円 | 100,000円 | 150,000円 | 40,000円 | 450,000円 | -40,000円 |
このように、製番ごとの原価推移や進捗を見ながら、「今、どこでコストが膨らんでいるのか」「赤字案件をどうカバーするか」など、経営に直結する判断が可能になります。
3)経営者・管理者にとっての“見える化”の価値
ERPによって原価情報が「見える化」されると、現場だけでなく経営層にも大きなメリットがあります。
経営判断の迅速化:案件ごとの収益状況を即座に把握し、投資・値引き判断に活用できる
予実管理の精緻化:見積と実績を突き合わせ、次の案件での見積精度を向上できる
戦略的受注の判断:利益率が高い製品群や顧客を特定し、重点戦略を組みやすくなる
属人的な集計から脱却し、業務の延長線上で自然に蓄積される原価情報を“資産”として活かすことが、ERPによる原価管理の真価です。
5.見積から実績まで、一気通貫で管理する製番別原価の仕組み
ERPによる個別原価管理の最大の特徴は、「見積」から「実績」までの情報を一元管理できることです。
多くの中堅・中小製造業において、この“つながり”が欠如していることで、損益のズレや赤字案件の見逃しが発生しています。
ここでは、製番を起点とした一気通貫の原価管理プロセスがどのように機能し、どんな効果をもたらすのかを解説します。
1)「見積もり精度」が利益を左右する
製造業における利益の源泉は、見積段階にあります。
見積時に適正な原価を把握できなければ、誤った価格設定となり、赤字案件を受注してしまうリスクが高まります。
しかし従来の見積業務では、以下のような課題が散見されます:
課題 | 内容 |
---|---|
経験頼り | ベテラン担当者の勘や過去資料に基づく属人的な見積もり |
実績との乖離 | 過去の実績データが整備されておらず、精度検証ができない |
工数の見積もり不足 | 詳細な工程分析ができておらず、手間が過小評価される傾向 |
ERPによって過去の製番別実績(材料費、工数、外注費など)を見積もりに活用することで、見積精度を飛躍的に高めることが可能になります。
2)「予算」と「実績」をリアルタイムで比較
ERPでは、製番に紐づけて「予定原価」と「実績原価」をそれぞれ管理できます。
これにより、案件の進行中でも損益の乖離をリアルタイムに把握し、対策を講じることができます。
このように「予算 vs 実績」の構造を案件ごとに可視化することで、
なぜ工数が多くかかったのか
材料費が高騰した要因は何か
といった“次に活かせる反省材料”が得られるようになります。
3)「製番別のPDCA」が業務改善を加速させる
ERPによる一気通貫の原価管理が定着すると、自然と製番別にPDCAを回す文化が生まれます。
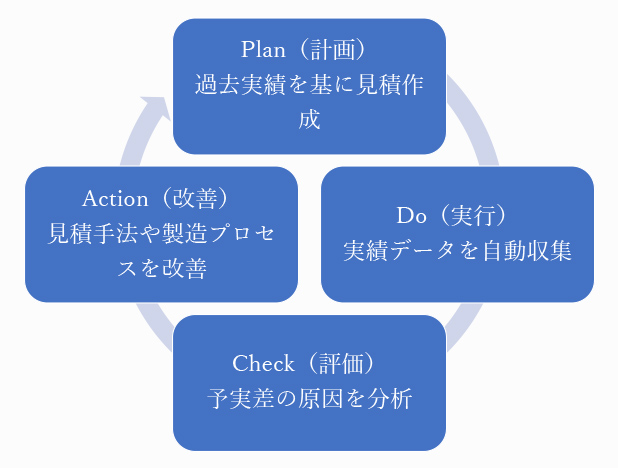
これにより、見積精度の向上 → 利益率の安定化 → 経営の強化という好循環が築かれていきます。
このように、ERPの原価管理は「結果を記録する」だけの仕組みではなく、「事前に利益を設計し、確実に利益を守る」ための“攻めの経営ツール”なのです。
6.導入事例に学ぶ!現場が変わり、経営が変わった中堅製造業の実践例
個別原価管理の必要性やERPによる実現手段を理解しても、実際に「うまく運用できるのか?」と不安を抱く企業は少なくありません。
ここでは、ERPによって製番別原価管理の高度化に成功した中堅製造業の実例を取り上げ、導入前の課題、導入の工夫、導入後の成果について紹介します。
1)電気機械器具製造業メーカー(従業員1,000名)
課題
- 案件ごとの損益が見えず、「手間がかかる割に儲かっていない案件」が後から発覚
- 現場ではExcelによる個別管理、経理部門では別システムでの費用集計と情報が分断
- 経営会議では属人的な勘に頼った判断が中心だった
ERP導入の工夫
- 製番別に「見積原価」と「実績原価」を登録・比較できる仕組みを構築
- 作業指示・購買・実績入力を現場で完結できるよう、業務フローを見直し
- 原価項目ごとに入力者を明確化し、ルールと教育を並行して展開
導入後の成果
項目 | Before | After |
---|---|---|
製番別損益の把握 | 案件終了後に月単位で手作業集計 | 案件進行中でもリアルタイムに損益を把握 |
利益率のばらつき | 一部案件で赤字に気づかず継続 | 赤字リスクを早期発見・対策可能に |
経営判断の精度 | 経験と勘が中心 | 定量データをもとに経営判断 |
これらの事例からわかるのは、ERPによる原価管理は単なるシステム導入に留まらず、
現場と経営が「同じ数字・同じ指標」で会話できる土台をつくるということです。
7.原価管理を定着させるERP導入のポイント
ERPの導入によって個別原価管理を実現するには、単にシステムを導入するだけでは不十分です。
「業務プロセスと現場意識を含めてどう変えていくか」が成否を分けるポイントになります。
ここでは、ERPによる原価管理を現場に定着させるために、実際の導入支援の現場で得られた知見などを参考にして「うまくいく企業の共通点」と「つまずきがちな落とし穴」を紹介します。
成功のカギ①:「原価情報を入力するのは誰か」を明確にする
原価情報は、現場・購買・経理など複数の部門を横断します。
そのため、誰が・いつ・どの項目を登録するのかを明文化しなければ、入力漏れや不整合が生じやすくなります。
例)
材料費 → 購買担当者が発注時に単価を登録
工数(作業時間) → 製造現場が実績入力端末で入力
外注費 → 購買担当者が納品時に実績原価を入力
このように、ERP上のデータと実際の業務の接点を一致させることが、正確な原価把握の前提条件です。
成功のカギ②:「原価を意識する文化」を育てる
ERPの導入だけで原価管理の精度が向上するわけではありません。
現場が原価を「自分ごと」として捉える文化を育てることが不可欠です。
たとえば…
- 毎月の会議で「製番別の原価予実」を共有し、部門横断で振り返る
- 赤字案件の要因分析を現場主導で行う
- 改善提案に対して評価やインセンティブなどを与える
ERPはあくまで「可視化の道具」です。それをどう活用して、現場に原価意識を根付かせるかがポイントです。
成功のカギ③:段階的にスモールスタートする
すべての原価情報を一度に管理しようとすると、現場の混乱や反発を招きやすくなります。
まずは試験的に特定の製品ラインや製番から開始し、運用とルールを固めたうえで全社展開するのが現実的です。
フェーズ | 内容 |
---|---|
Step1:パイロット導入 | 主要製品や一部部門に限定して導入。運用ルールを検証・改善 |
Step2:横展開 | 他部門や他製品に展開。運用の標準化・マニュアル化 |
Step3:全社展開 | 全社的な製番別原価管理へ統合。経営指標として活用 |
このように段階的に展開することで、社内理解や業務フローの整理も進み、ERP活用の成熟度が高まります。
避けるべき落とし穴:「導入=ゴール」と考える
ERP導入において最も避けたいのが、「導入=完了」と捉えてしまうことです。
原価管理の仕組みは導入して終わりではなく、「どう使い続けるか」が真価を問われるフェーズです。
運用開始後に見えてくる課題や改善の芽を放置してしまうと、せっかくのシステムが“使われない仕組み”になってしまいます。
よくある失敗例:
- 一部の担当者しか使わず、現場での定着が進まない
- マスター更新が追いつかず、信頼されない原価情報になる
- 現場からのフィードバックを取り入れず、“上からの仕組み”になってしまう
ERPによる個別原価管理の定着には、人・業務・文化の変革が欠かせません。
「正しい情報を正しく入力する仕組み」「現場が活用できる設計」「段階的な運用拡大」といった視点を持つことで、原価管理が単なる業務負担ではなく、会社を強くするための武器へと変わっていきます。
8.これからの製造業に求められる原価管理―“見える化”から“利益体質”へ
激変する市場環境の中で、中堅中小製造業が生き残り、持続的に成長していくためには、単なる「原価の見える化」にとどまらず、原価管理を通じて「利益体質への変革」を実現することが求められています。
1)原価管理の役割は「経営の羅針盤」
原価を詳細に管理することは、コスト削減や無駄の排除といった狭い意味だけでなく、経営判断の精度を高める羅針盤の役割を果たします。
「どの製品が利益を生み、どの案件がリスクを抱えているのか」をリアルタイムに把握できれば、迅速で的確な意思決定が可能となります。
2)市場変化に対応する柔軟な経営体制へ
市場の多様化やグローバル競争の激化、原材料価格の変動など、外部環境の変化は予測困難です。
個別原価管理を通じて製番単位の利益状況を把握できれば、以下のような柔軟な対応が可能です。
- 赤字案件の早期中止や再交渉
- 利益率の高い製品への資源集中
- 価格戦略の見直しやコスト構造の改善
こうした迅速な経営判断は、競争優位を維持するために不可欠です。
3)「攻めの原価管理」で競争力を高める
単なるコストカットではなく、利益を最大化するための「攻めの原価管理」へシフトすることが重要です。
ERPで得られる正確なデータを活用し、
- 新規案件の見積精度向上
- 製造プロセスの効率化や歩留まり改善
- 品質向上による再作業・クレーム低減
など、経営戦略の一環として原価管理を活用する企業が増えています。
4)IT投資と人材育成の両輪で強化を
高度な原価管理はITシステムだけで実現できるものではありません。
社員一人ひとりが数字に強くなり、現場で改善活動を推進できる人材育成も欠かせません。
項目 | 施策例 |
---|---|
IT環境 | ERPの継続的なアップデート、モバイル端末や製造現場でのIoT活用などによる業務負荷軽減 |
教育・研修 | 原価意識向上のための勉強会や改善ワークショップの実施 |
仕組み | KPI設定と評価制度の連動、改善提案のインセンティブ化 |
9.まとめ
変化の激しい製造業の経営環境の中で、個別原価管理は経営の「見える化」を超え、「利益を生み出す経営基盤」へと進化しています。
中堅中小製造業が競争力を維持・強化するためには、ERPを活用した原価管理の導入・定着はもはや必須だと言えます。
※記事の内容は、制作時点に一般公開されている情報に基づいています。また、記載されている会社名・製品名・システム名などは、各社の商標、または登録商標です。