SRMとは何か?製造業におけるサプライヤー戦略の重要性
1.SRM(サプライヤーリレーションシップマネジメント)とは
SRM(Supplier Relationship Management)は、直訳すると「サプライヤーとの関係性を管理すること」です。もう少し噛み砕くと、「自社の調達先であるサプライヤーと、戦略的かつ協調的な関係を築くことで、安定した供給とコスト競争力を確保し、製造業としての競争力を高めていく活動」と言えます。
従来、調達や購買の業務は「いかに安く仕入れるか」という視点が中心でした。しかし、現在ではそれに加えて「品質」「納期」「サステナビリティ(持続可能性)」「リスク対応力」など、多面的な視点でのサプライヤーとの関係性が求められるようになっています。
SRMは、単なる購買管理ではなく、サプライヤーを“パートナー”として捉え、双方向のコミュニケーションや協業を通じて、長期的な価値を創出することを目的としており、近年注目されています。
2.なぜ今、SRMが注目されているのか?
(1)サプライチェーンの複雑化とリスクの顕在化
グローバル化の進展や、自然災害、パンデミック、地政学的リスクなどにより、サプライチェーンの寸断リスクが顕在化しています。
(サプライチェーンが分断され、製造に大きな影響を与えた事例)
時期 | 種類 | 影響を受けた産業 | 内容 |
---|---|---|---|
2011年 | タイ大洪水 | 自動車、電子部品、HDDなど |
タイは多くのグローバル製造業にとって「アジアの生産拠点」でした。ハードディスクドライブ(HDD)の生産拠点が集中しており、大規模な洪水で多数の工場が浸水・操業停止。結果として、HDDの世界供給量が約30%減少し、パソコンメーカーなどにも深刻な影響があった。 日本の自動車メーカー(トヨタ、ホンダなど)も現地サプライヤーからの部品供給の停止により、国内外の工場での生産停止を余儀なくされた。 |
2020年~ | 新型コロナウイルス感染症 | 自動車、半導体、医薬品など |
中国・武漢にはじまる都市封鎖(ロックダウン)により、自動車部品の供給が滞り、トヨタ、日産などの工場で一時的な稼働停止が発生。 世界的に半導体の需給が逼迫し、車載用半導体が不足。トヨタやフォード、ホンダなど多くの自動車メーカーが減産。 医療用マスクや消毒液、ワクチンなどの供給も混乱し、サプライチェーンの脆弱性が一気に顕在化した。 |
2020年 | 九州豪雨 | 電子部品、自動車関連など |
九州地方での豪雨により、複数の電子部品メーカーの工場が一時操業停止となった。 自動車メーカーの生産にも波及。特に、重要な電子部品を供給する中小の一次・二次サプライヤーが被災し、調達網が途切れた。 |
このように製造業にとって、部品や原材料の安定供給が事業継続の生命線である以上、信頼できるサプライヤーとの関係構築は、企業のリスクマネジメントとしても重要な意味を持っています
(2)競争力強化の鍵としての「協調型サプライチェーン」
製品ライフサイクルの短期化により、市場ニーズへの迅速な対応が求められています。その中で、サプライヤーと情報を共有しながら製品開発や生産計画、販売を進める「協調型サプライチェーン」が注目されています。SRMを導入することで、サプライヤーとより緊密に連携し、競争力ある製品をタイムリーに市場に届ける体制を構築できます。
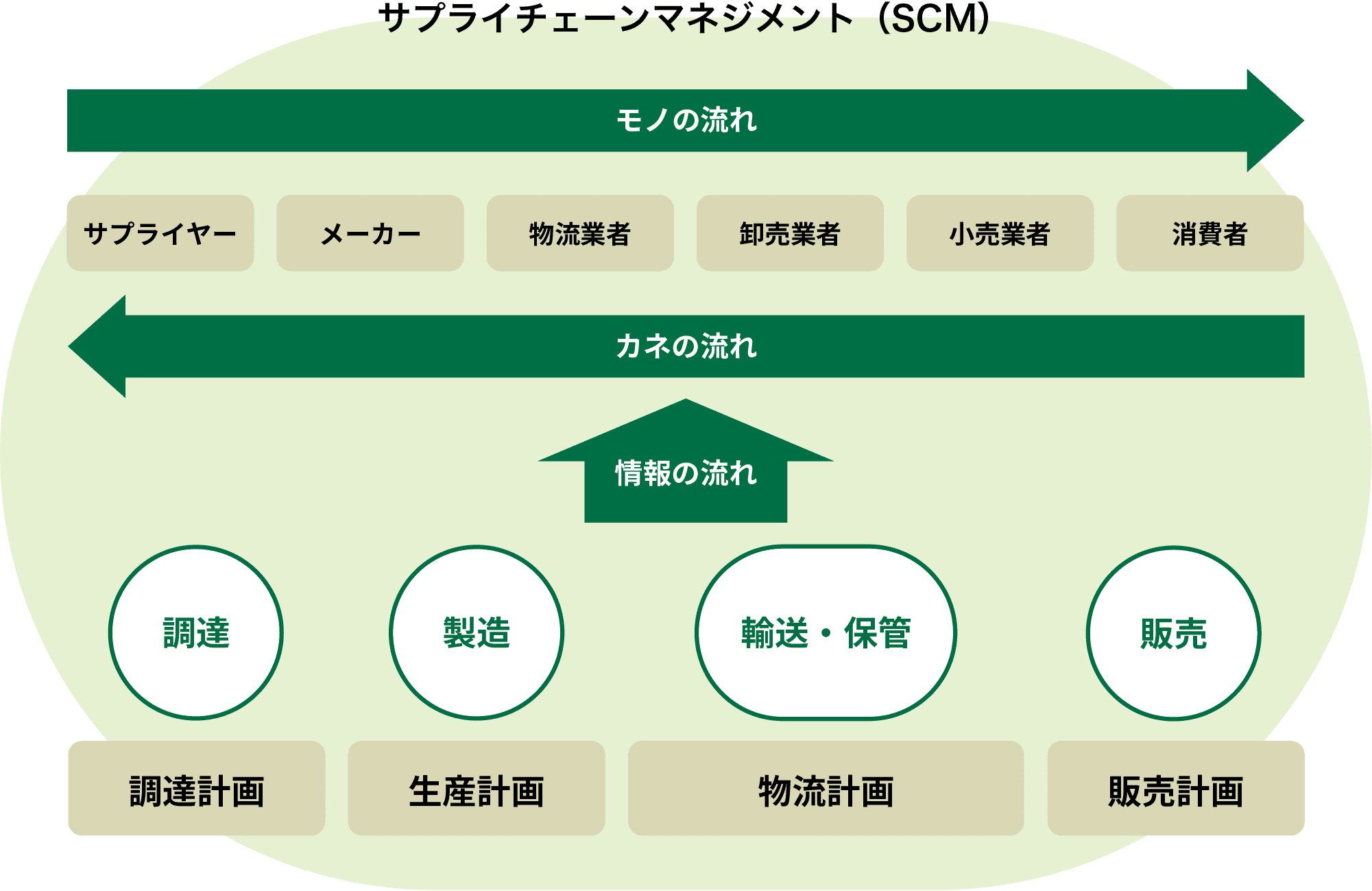
(3)サステナビリティやCSRへの対応
近年は、調達活動においても環境・社会・ガバナンス(ESG)への配慮が求められるようになってきました。特にグローバル企業では、「どのような企業から、どのように調達しているのか」が取引先選定の重要な基準となっています。SRMを通じてサプライヤーに対してESG方針を共有し、改善活動を支援することは、企業の持続的成長にも直結します。
(例)サプライチェーン排出量とは?
サプライチェーン排出量は、自社内における直接的な排出だけでなく、自社事業に伴う間接的な排出も対象とし、事業活動に関係するあらゆる排出を合計した排出量を指します。
つまり、原材料調達・製造・物流・販売・廃棄など、一連の流れ全体から発生する温室効果ガス排出量のことです。
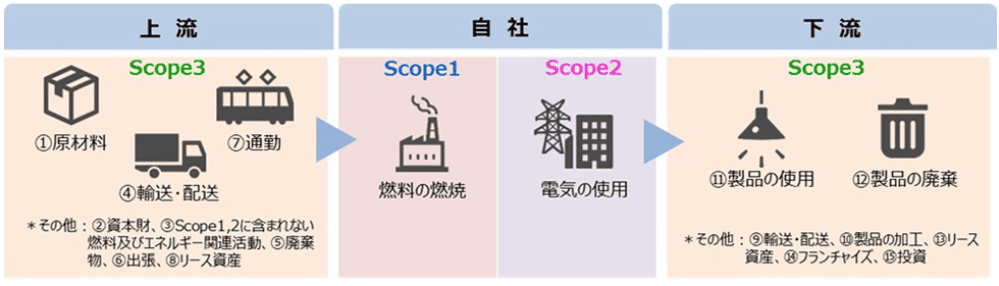
環境省HP:グリーン・バリューチェーンプラットフォームより転載
https://www.env.go.jp/earth/ondanka/supply_chain/gvc/estimate.html
3.SRMの具体的な取り組み内容
SRMは一過性の施策ではなく、継続的な改善サイクル(PDCA)を回しながら進めていくことが重要です。以下は一般的なSRMの取り組み例です。
(1)サプライヤーの分類と評価
まずは既存のサプライヤーを、「取引規模」「重要度」「リスク」などの観点から分類・評価します。戦略的に重要なサプライヤーには重点的に対応し、協業関係を深めていきます。
以下に、サプライヤーを重要度とリスクで分類したマトリックスを紹介します。
このようなマトリックスは、SRMの出発点として有効です。
(例)サプライヤー分類マトリックス(重要度 × リスク)
高重要度 | 低重要度 | |
---|---|---|
高リスク |
① 戦略的ハイリスクゾーン ・本来内製すべきもので、代替困難、事業に重大な影響あり ・外部から供給を受ける場合はサプライヤーとの共同開発など強固なパートナーシップを構築 |
③ リスク管理ゾーン ・十分な安全在庫を確保する ・安定的な調達のため継続的な供給契約を締結するなど、サプライヤーとの関係構築が重要 |
低リスク |
② 要注意ゾーン ・低リスクだが重要性は高い ・複数サプライヤーから相見積りを取り、代替調達手段を確保しつつ、安価なサプライヤーから調達 |
④ 日常管理ゾーン ・一般購買品や汎用品などが主な対象 ・必要な時に必要な量を調達する |
※リスクの視点:自然災害、地域依存、財務状況など
※重要度の視点:製品構成上の位置づけや代替可能性などで判断
(2)KPI設定とモニタリング
納期遵守率、不良率、コスト削減率など、調達に関わるKPIを設定し、定期的にモニタリングし、サプライヤーのパフォーマンスを可視化します。
(KPIの例)
カテゴリー | KPIの例 |
---|---|
コスト | コスト削減率、コスト回避額、単価変動率 |
品質 | 受入検査不良率、クレーム発生件数、品質改善率 |
納期 | 納期遵守率、納期遅延平均日数、緊急対応発生件数 |
サプライヤーパフォーマンス | 改善提案件数、年間達成率 |
(3)双方向のコミュニケーションの強化
定期的にレビューやミーティングなどを設け、情報を共有することで、サプライヤーとの信頼関係を構築します。単なる成果報告だけでなく、課題共有や改善提案の場としても機能させることが双方の信頼関係の強化には重要です。
(4)ITの活用による情報の一元管理
SRMシステムやERPなどにシステムに組み込まれた調達管理モジュールを活用することで、調達情報の一元化、文書管理、契約管理などを効率化できます。自動モニタリングで収集したデータに基づく意思決定が可能になるため、環境変化による調達方法の見直しなど、より戦略的な調達が実現します。
4.SRM導入に向けたステップ
SRMは導入すればすぐに成果が出るものではなく、段階的なステップを踏みながら社内に定着させていくことが求められます。
ステップ1:現状把握と課題整理
自社の調達業務やサプライヤーとの関係性を見直し、改善すべきポイントを洗い出します。
ステップ2:SRMの目的と方針を明確化
経営層を含めて、SRMを導入する目的や期待効果を共有し、社内全体での合意形成を行います。
ステップ3:体制の整備とツール導入
SRMを推進するための担当部門・担当者を明確化し、必要に応じてITツールの選定・導入を行います。
ステップ4:パイロット運用と評価
まずは一部の重要サプライヤーを対象にSRMを試験的に導入し、その効果を評価します。
ステップ5:全体展開と継続的な改善
得られた知見をもとに対象範囲を広げ、全社的な仕組みとしてSRMを定着させていきます。
5.サプライチェーン強化を実施したERP導入事例
株式会社マツオカコーポレーション様は、アパレル製品の製、洗い加工、生地開発、生産を一手に手掛けるOEM専業の総合アパレルメーカー。年間取り扱い点数は1300万点におよび、関連会社も含め中国を中心に海外15カ所へ工場を展開。
受注、資材調達、生産、納品まで、すべての段階における資材の調達状況や生産の進捗状況、そして在庫情報をリアルタイムで管理できる、SCMをサポートするシステムの実現が重要だと考え、ERP「GRANDIT」を導入し、経営情報をリアルタイムで確認できるようになり、SCMの効率化を実現しました。
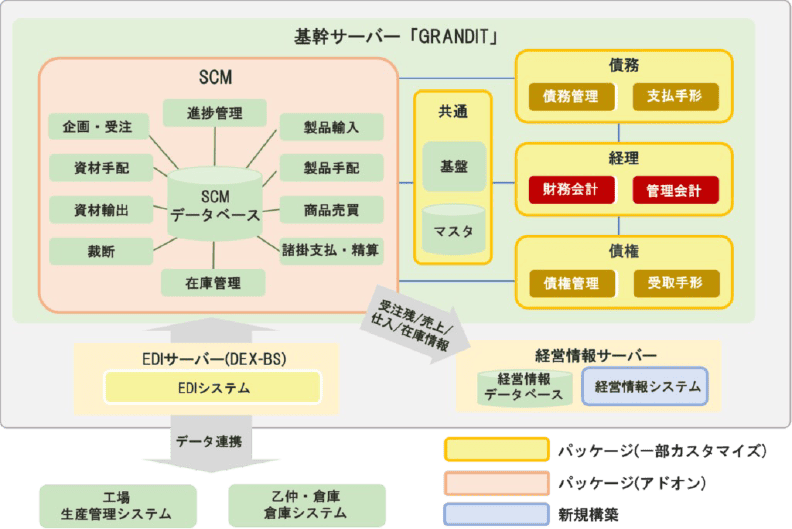
【導入事例】株式会社マツオカコーポレーション様
https://www.grandit.jp/showcase/detail/matsuoka.html
SRMは、単にサプライヤーを管理する仕組みではなく、企業の競争力を高めるための重要な経営戦略です。製造業においては、調達の現場だけでなく、経営、製造、品質、ITといった多部門が連携して進めていくことが成功の鍵となります。
これからSRMに取り組むにあたっては、まずは「なぜSRMが必要なのか?」という共通認識を社内で持つことが第一歩です。その上で、自社の業務に合った形で、無理なく段階的に進めていくことが大切です。
※記事の内容は、制作時点に一般公開されている情報に基づいています。また、記載されている会社名・製品名・システム名などは、各社の商標、または登録商標です。
ERPコラム一覧
ITと業務による両立
プロジェクト推進方法 その1
プロジェクト推進方法 その2
-働き方改革を実現するには-